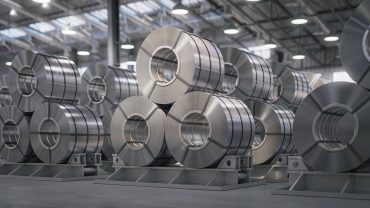
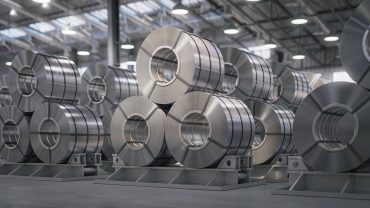
Steel industry decarbonization gains momentum as Boston Metal’s electrolysis process demonstrates commercial viability for sustainable manufacturing
Key Takeaways
- Boston Metal achieves commercial breakthrough with successful commissioning of its multi-inert anode MOE industrial cell in March 2025, demonstrating scalability for producing 1-2 tons of steel monthly.
- Steel industry emissions reduction targets 11% of global CO2 as molten oxide electrolysis offers zero-carbon alternative to traditional blast furnaces, requiring only 4 megawatt-hours per ton of steel.
- Commercial deployment timeline set for late 2026 with Boston Metal planning demonstration facilities and global technology licensing to steelmakers, targeting $1,000 per annual ton capacity investment.
Introduction
The global steel industry faces mounting pressure to eliminate carbon emissions as demand softens and environmental regulations tighten. Steel production generates approximately 11% of worldwide carbon dioxide emissions, making decarbonization a critical business imperative for manufacturers.
Boston Metal has achieved a significant milestone in zero-carbon steelmaking with its molten oxide electrolysis technology. The Massachusetts-based company successfully commissioned its industrial-scale MOE cell this month, demonstrating the process can produce steel without coal-based fuel or carbon emissions.
“We are the only company with a direct and scalable approach to more efficient and clean steelmaking,” said Tadeu Carneiro, CEO of Boston Metal. The breakthrough addresses the industry’s largest environmental challenge while potentially reducing production costs.
Key Developments
Boston Metal commissioned its multi-inert anode MOE industrial cell at its Woburn, Massachusetts facility in March 2025. The system demonstrates the technology’s scalability and reliability for commercial applications, producing one to two tons of steel monthly.
The company operates its emissions-free process adjacent to a daycare center, highlighting the clean nature of the technology. “It just proves how different the future of steel can be,” said Adam Rauwerdink, Boston Metal’s senior vice president for business development.
Molten oxide electrolysis uses electrical current to directly reduce iron oxide into molten iron and oxygen at approximately 1,600°C. The process eliminates carbon-based reductants entirely, producing pure oxygen gas instead of carbon emissions when powered by renewable electricity.
The technology originated at the Massachusetts Institute of Technology and addresses critical limitations of traditional steelmaking. Unlike blast furnaces that require premium iron ore grades, MOE can process all ore qualities, providing manufacturers greater raw material flexibility.
Market Impact
The steel industry’s decarbonization efforts have accelerated as global demand softens and environmental costs increase. Traditional steelmaking faces rising expenses from carbon credits, emission controls, and regulatory compliance.
Boston Metal’s modular approach allows incremental technology adoption. Each electrochemical cell produces up to 10 tons of steel daily, enabling both large producers and mini mills to deploy the technology without massive upfront investments.
The company targets cost competitiveness with conventional steelmaking when electricity prices remain around $20 per megawatt-hour. This pricing structure aligns with declining renewable energy costs and creates potential cost advantages over coal-based production.
Economic analysis suggests MOE plant investments may resemble aluminum smelter operations, with estimated costs of $1,000 per annual ton capacity. This represents significant capital savings compared to traditional blast furnace infrastructure.
Strategic Insights
Boston Metal’s business model centers on technology licensing rather than direct steel production. This approach allows rapid global deployment while minimizing capital requirements and operational risks for the company.
The technology’s electricity intensity creates both challenges and opportunities. Producing global steel volumes through MOE would require approximately 20% of current worldwide electricity consumption, necessitating massive renewable energy expansion.
Boston Metal diversifies revenue streams by targeting multiple metals beyond steel. The company prepares to establish a chromium metal facility domestically, securing critical materials for advanced manufacturing while generating near-term revenues.
The firm’s short-term strategy focuses on extracting niobium from mining waste and industrial slag. Niobium commands significantly higher prices than steel, providing financial stability during technology development phases.
Expert Opinions and Data
Industry stakeholders express significant enthusiasm for MOE’s decarbonization potential. The modular, scalable design attracts both established producers and new market entrants seeking clean production alternatives.
Technical challenges persist despite commercial progress. High operating temperatures strain material durability, while corrosive molten oxide electrolytes threaten structural integrity. CleanTechnica reports that ongoing durability and electrochemical stability issues require continued engineering solutions.
Investors and ESG-focused funds view MOE as foundational technology for sustainable industrial transformation. The prospect of cost parity with traditional steelmaking without subsidies represents a potential market disruption across metals industries.
Operational resilience remains critical, as power interruptions can cause severe “cell freeze” conditions. The technology requires robust electrical infrastructure, including heavy-duty transformers and backup power systems to maintain consistent operations.
Conclusion
Boston Metal’s successful MOE demonstration marks a pivotal moment for zero-carbon steelmaking. The technology offers a direct path to eliminating the steel industry’s massive carbon footprint while maintaining economic viability.
The company’s planned late-2026 demonstration facility and global licensing strategy position MOE for widespread adoption. Success depends on continued access to affordable renewable electricity and supportive regulatory frameworks that price carbon emissions appropriately.
MOE represents the convergence of environmental necessity and technological capability in heavy industry. The technology’s commercial viability could reshape global steel markets and accelerate industrial decarbonization across multiple sectors.