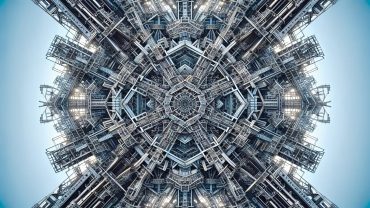
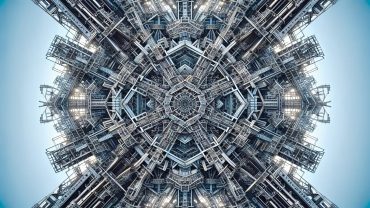
Australian green steel market emerges as global manufacturing shifts toward renewable energy-powered metal production
Key Takeaways
- Australia targets $250 billion green steel export market with annual revenues projected at $174 billion, backed by $5 billion in government funding and major projects including a $2.5 billion DRI plant.
- Hydrogen alternatives prove more cost-effective as molten oxide electrolysis, flash ironmaking with carbon capture, and biomethane-based production offer viable pathways without expensive hydrogen infrastructure.
- Government commits $4 billion through Hydrogen Headstart program plus $2 per kilogram tax incentive for green hydrogen production, signaling unprecedented policy support for the industry transition.
Introduction
Australia positions itself to capture a potential $250 billion green steel export opportunity as global steelmaking faces unprecedented transformation. The nation’s vast iron ore reserves, abundant renewable energy resources, and feasible carbon sequestration sites create unique advantages for low-emission steel production.
This strategic pivot comes as global primary steel demand levels off, driven largely by China’s construction slowdown. The shift forces steelmakers worldwide to prioritize cost-efficient, environmentally sustainable production methods over traditional carbon-intensive processes.
Key Developments
The Australian government earmarks up to $3 billion from the National Reconstruction Fund for renewables and low-emissions technologies. An additional $1 billion focuses specifically on value-adding in resources, moving beyond traditional iron ore exports.
Major projects demonstrate this commitment through concrete investments. Green Steel of Western Australia launches a $400 million recycling mill alongside plans for a $2.5 billion direct reduced iron plant. The Collie mill expects to produce 450,000 tonnes annually of green rebar and wire rod.
The government introduces comprehensive policy support including a $2 per kilogram tax incentive for green hydrogen production. This refundable tax offset operates for up to ten years between 2027 and 2040 for projects reaching final investment decisions by 2030.
Market Impact
Green steel production addresses immediate market pressures as global automakers sign international offtake agreements. These commitments signal robust future demand while helping companies avoid carbon border adjustment tariffs from major trading partners.
The low-emission hydrogen market projects growth from $1.4 billion today to $12 billion by 2030 globally. Australia’s green metals sector could reduce domestic emissions by up to 11%, supporting the national target of 43% emissions reduction by 2030.
Investment flows increasingly favor green steel projects as they align with global decarbonization trends. The sector benefits from reduced regulatory uncertainty through government procurement policies requiring minimum green steel percentages in public infrastructure projects.
Strategic Insights
Three distinct production pathways emerge as economically viable alternatives to hydrogen-based steelmaking. Molten oxide electrolysis directly uses electricity to split iron ore, eliminating carbon emissions without requiring expensive hydrogen infrastructure. This method suits regions rich in solar and wind resources.
Flash ironmaking with carbon capture proves practical in areas with cheap natural gas access. The process rapidly heats iron ore particles while capturing emissions, particularly viable in regions like the Cooper Basin with suitable geology.
Electrified biomethane-based direct reduced iron combined with carbon capture suits agricultural regions with abundant waste biomass. This approach provides negative emissions solutions while remaining economically competitive under current carbon pricing.
Expert Opinions and Data
Dr Ross Garnaut, former Australian Ambassador to China, emphasizes the scale of opportunity. “Japan, Korea, and China import huge quantities of Australian iron ore and coal and put them together to make iron metal, releasing greenhouse gases as a waste,” he explains. “Conversion of Australian iron ore into iron and steel produces about 4 percent of the world’s greenhouse gas emissions—more than three times the emissions from everything we do in Australia.”
According to Renew Economy, Australia’s credible zero-carbon steel opportunity rests on process innovations beyond hydrogen dependency. Industry analysis reveals hydrogen direct reduced iron remains cost-prohibitive, with current estimates placing costs substantially higher than alternative methods.
Garnaut advocates for robust government support for innovation. “We don’t get enough innovation unless governments provide financial support for it,” he states. The government responds with the $4 billion Hydrogen Headstart program providing revenue support for large-scale projects through competitive production contracts.
Conclusion
Australia’s green steel strategy integrates existing resources and emerging technologies to establish global leadership in low-emission metals production. The approach prioritizes economically viable pathways while building infrastructure for future hydrogen integration.
The transition requires unprecedented coordination between governments, industry, investors, and civil society. Current policy frameworks and investment commitments position Australia to capture significant export opportunities while meeting domestic climate targets and avoiding international trade barriers.